 |
Feb 2005 through May 2005 Update
(Note: Subscribers to the email list receive the update earlier
than it is posted on the website. Email address privacy is always respected.)
[September 26: Target launch date for Falcon I maiden flight is October 31 from our island launch complex in the Kwajalein Atoll.
The customer for this mission is DARPA and the payload will be FalconSat-2, part of the Air Force Academy’s satellite program that will measure space plasma phenomena, which can adversely affect space-based communications, including GPS and other civil and military communications.
Our second mission carrying TacSat-1 for the Naval Research Laboratory will follow the last Titan IV launch from VAFB.]
Fire on the Launch Pad!
As you may have read, we test fired Falcon I on our launch pad at Vandenberg Air Force Base. Vandenberg, for those that don’t know it, is the primary US launch site for polar or close to polar orbits and is located about a third of the way up the California coast. The five second test was picture perfect this time around, starting on schedule at 9:00:00 am and finishing at 9:00:05 am.
The two prior attempts aborted with the first abort being due to an igniter sensor failure and the second due to an incorrectly closed helium ground supply valve. The igniter was actually working properly (we could see the puff of smoke it produced on camera), but without the computer being able to detect ignition, it would have been too risky to proceed. We have now changed the location of the sensor to make it less susceptible to damage from the ignition event and it is working flawlessly so far.
The purpose of this firing was an overall systems check for the vehicle and the ground support equipment and it was really quite a smooth process, all things considered. One bug in the vehicle and one bug in the launch pad support system is pretty minimal for a new rocket from a new pad.
Assuming that there are no further delays in the last Titan IV rocket, which is scheduled to depart from Vandenberg in July, we expect to receive a Falcon I launch window in the August timeframe. Our flight path poses a small, but non-zero hazard for the Titan IV, which is a multi-billion dollar mission.
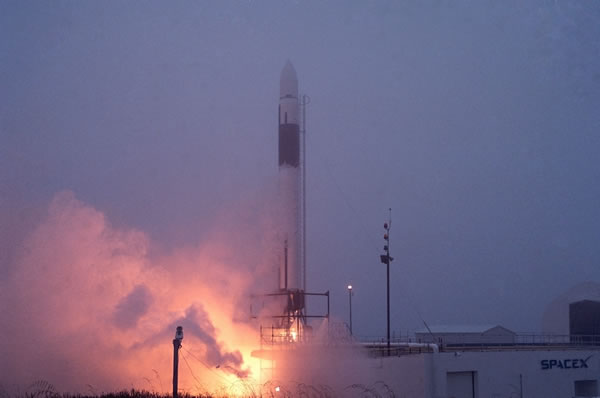
Video of Falcon I on the Launch Pad
Business is Good
The Air Force awarded us a contract for Falcon I launch services valued at up to $100 million (depending on how many launch options are exercised), which is a pretty significant endorsement. This is independent of the DARPA/Air Force FALCON program, for which we are doing a launch later this year from our launch complex in the Marshall Islands.
There are also a number of other customer discussions that are quite mature. It appears quite likely that we will receive one or two more launch contracts over the next few months. Given how strong demand is at this early stage of the game (we have three launches scheduled in the next six months), I think we will have no problem reaching our goal of an annual launch rate of 5+ per year in a few years.
Not yet mentioned on our manifest or in any press release is our classified launch business, for obvious reasons. There is not much I can say about this, except that the dollar value exceeds all unclassified business combined, excluding the AF $100M contract.
NASA Space Act Agreement
Credit goes to the folks at the NASA Johnson Space Center for very quickly drafting and executing a Space Act Agreement with SpaceX. JSC is the primary NASA center for human spaceflight and, since human transportation is the primary long term goal of SpaceX, we are likely to be doing a lot of work in partnership.
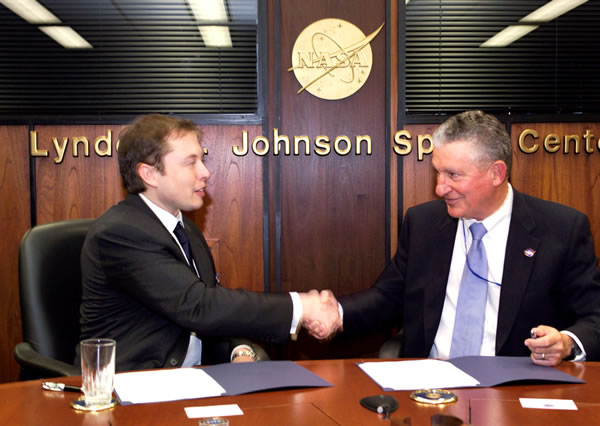
Signing the Space Act Agreement with Beak Howell, Director of NASA JSC
This agreement provides a legal framework for interchange of personnel, information and resources. Now that development of Falcon I is almost over, we are turning our focus to Falcon V, and one of the primary markets for that vehicle is resupply of the International Space Station. As such, we will need to work closely with JSC and other parts of NASA to understand the rendezvous and docking/berthing requirements.
Growing SpaceX to Meet Demand
SpaceX is undergoing a significant transformation in 2005 from a company that does R&D to one that does R&D, manufacturing and launch operations. Moreover, with the development of Falcon V and a few secret projects we have on the go, we are also increasing the scope and scale of the R&D.
We have tripled in size from a year ago and are now at about 130 employees. Real estate includes 80,000 sq. ft. of office & manufacturing space in the L.A. area, a 300 acre test facility in Texas and an office Washington D.C., as well as launch complexes at Cape Canaveral, Vandenberg and the Marshall Islands. A number of new executives have joined the company, including Jackie Nesselroad, who was running Delta IV production for Boeing and Ray Miryekta, formerly Boeing’s chief weld engineer.
TECHNICAL UPDATES
Falcon I development is essentially complete, although we will continue to do testing and retesting (it never really ends) right up to the day of launch. Therefore, the technical updates section will now talk about Falcon V.
Propulsion
For the Falcon V first stage, we are developing some modest upgrades to the Merlin 1A engine and calling it Merlin 1B. The target specifications are:
Sea level thrust: 85,000 lbf
Vacuum thrust: 99,000 lbf
Chamber pressure: 890 psia
Sea level Isp: 261 sec
Vacuum Isp: 303 sec
Changes to the core of the engine are minimal:
-
More turbine nozzles to develop 2500 HP vs. the current 2000 HP
-
Stronger pins connecting the turbine wheel to the turbopump shaft to transfer the extra power.
-
New main liquid oxygen valve with a wider opening. The current valve is too small and restricts the flow.
-
Bell mouthing the fuel main line where it joins the fuel manifold. This should improve fuel distribution in the chamber.
-
Changing to TEA-TEB (pyrophoric) ignition, which we already use on the Kestrel engine, from torch ignition. There is just too much to go wrong with a torch igniter, whereas TEA-TEB is a lot simpler. Historically, most LOX/RP engines, such as the Saturn V F-1, have used TEA-TEB.
Since we have multiple engines on the first stage and thus no longer need individual roll control on each engine, we are removing that system for the M1B. Removal of that system combined with manufacturing efficiencies will make the M1B considerably lower cost than M1A, despite delivering more thrust.
We currently have twelve M1B engines in the manufacturing cycle, with six due to be completed in August and another six in December. Each engine will be individually tuned and acceptance tested and then integrated into the main thrust frame of the stage. If things go reasonably well, we will complete a stage hold down firing with all engines on the giant tripod test stand by the end of this year.
Structures
Things are moving along well in building up the Falcon V primary structures and I’m increasingly confident that we will achieve significant breakthroughs in cost. A few of the more significant factors contributing to this are:
-
Since both stages operate at the same pressures and use the same propellants, we are able to make the 2nd stage simply be a truncated version of the 1st stage (just fewer barrel sections). In both cases you are feeding Merlin engines, so stage systems are almost identical. This means only one set of tooling and one manufacturing process to optimize.
-
Our barrel sections are constructed from rolled aluminum sheet with stringers stir welded in for stiffness. This method yields substantial cost savings over the conventional launch vehicle approach of using machined isogrid. With isogrid and its variants, you start with a plate of aluminum that can be as thick as two inches and then machine away up to 90% of the material, leaving behind sheet with integral stiffeners. This is obviously very inefficient use of material and requires thousands of hours of machining time.
In our use of the same structural architecture and engine (Merlin) for both the 1st and 2nd stage of Falcon V, SpaceX is using the same tactics of consistency to reduce cost employed by Southwest Airlines, who uses only Boeing 737 airplanes.
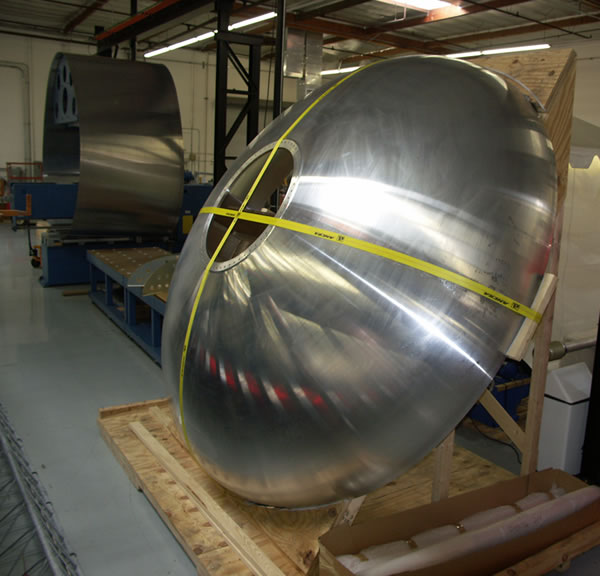
A 12 ft diameter dome
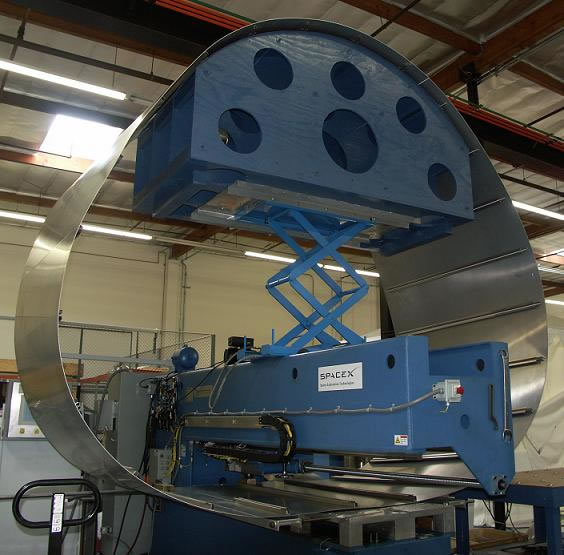
A 12 ft diameter barrel section with stir welded stringers (rounding hoops to be added)
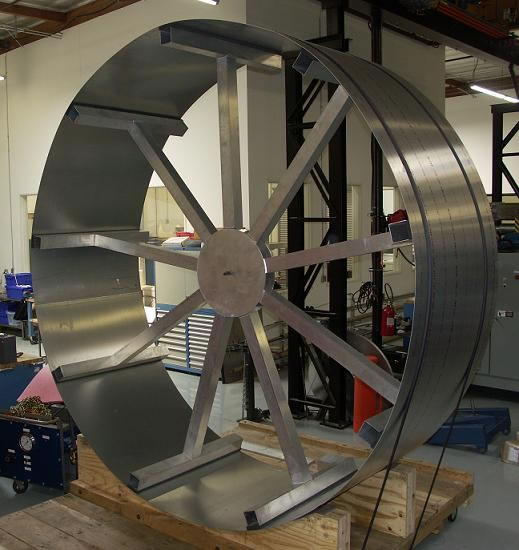
A barrel section in its holding fixture
Avionics, Guidance & Control
Our engine control electronics will be much more integrated for the Merlin 1B than 1A. Instead of having several separate electronics boxes for engine valves, thrust vector control, sensors, mixture control and so forth, it will all be combined into one very well protected engine control unit with more integrated electronics. This should both increase reliability by getting rid of interconnecting wires and decrease cost.
We are also moving to a more digital system. There will be no analog wiring between the engine and stage – the only wires leading out of the engine control unit to the stage are a pair for power and a pair for Ethernet. This gives the engine a very modular, plug-and-play capability. Connecting it up to the stage for power & data will be about as hard as plugging in your laptop.
Our overarching goal is to have a system that is safe enough for humans and can remain in orbit for an extended duration. Therefore, the general principle we are following is to seek triple redundancy on components where soft failures are possible and hard to detect (RAM, IMU, etc) and dual redundancy where hard failures are the only realistic possibility.
We have run a number of flight simulations against our control algorithms, including shutting off engines at inopportune times. The system appears robust enough to handle engine out with no problem. If we do lose an engine, we would like to adjust the guidance system to maintain a low angle of attack trajectory that is as close to optimal as possible. Various schemes are being considered, from “multiple nominals” to an engine out correction angle to an additional lateral velocity loop. The latter is our current preference.
----- Elon ----
< Archived Updates
|
 |